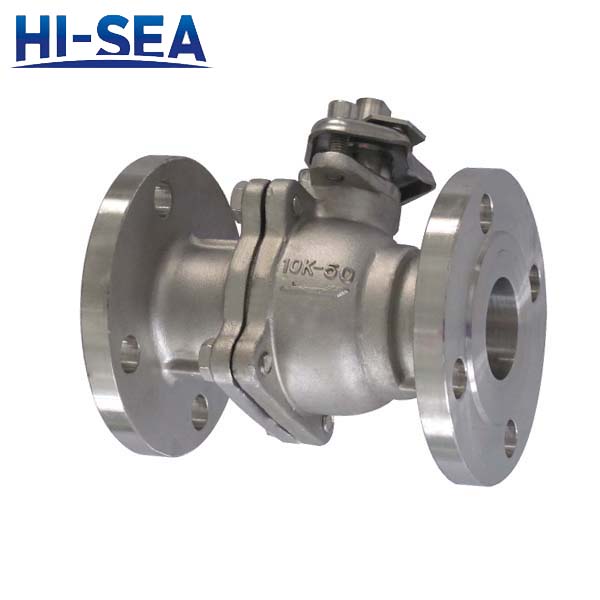
Power Station Drain Ball Valve
Introduction:
Drain ball valve of power station: also known as high temperature and high pressure drain valve, floating welded ball valve, self sealing structure, manual / electric / pneumatic, metal sealing, pressure PN64 ~ PN450, through DN15-DN100.
Purpose:
Make full use of dry high-temperature, high-pressure and high solid content media, wear-resistant and corrosion-resistant working conditions, including power plants, petrochemical and mining industries. Boiler drainage, steam turbine drainage, boiler regular and continuous drainage of water supply system, steam drum drainage, superheater drainage and drainage, soot blower isolation, bypass pipeline isolation, economizer header drainage.
Features:
1. The company has successfully developed high-temperature and high-pressure ball valves through optimized design, which can reach the pressure level of 4500lb and the high temperature of 650 ° C, and solve the high-temperature and high-pressure conditions of steam, gas, coal cinder, slurry, heavy oil and other special media and the application of wear-resistant media of pulverized coal.
2. HVOF thermal spraying technology and supersonic spraying technology solve the reliability and integrity of spraying materials from the technical analysis of three elements: binding force, porosity and hardness, so that the hardness of the sealing surface of the ball and valve seat reaches above HRC78, and the service life and anti-wear capacity of the valve are improved.
3. The valve stem seal adopts dynamic disc and other loading structures, which ensures the tightness of the valve stem, reduces the friction of the packing of the valve stem, and reduces the torque of the valve switch.
4. The sealing surfaces of the valve seat and the ball are subject to one-to-one directional grinding with carborundum, which makes the sealing more consistent, improves the sealing performance, and achieves zero leakage of the valve.
5. Independently developed and developed a high-temperature wear-resistant test bench to simulate harsh working conditions to conduct type tests on valves to ensure the sealing performance and valve switching flexibility under high-temperature and high-pressure conditions.
6. The valve adopts pneumatic, electric, electro-hydraulic linkage, turbine drive and handle operation.
7. Finite element analysis of valve stress.
Drawing:
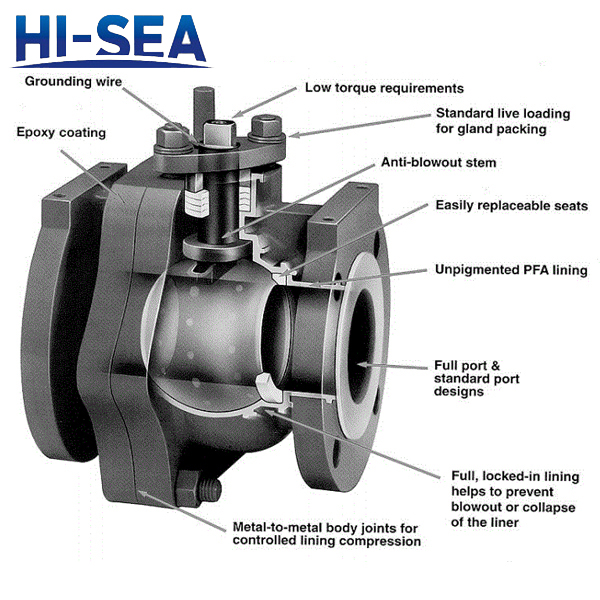